Measure steps to reduce air consumption
Ultra –sonic cleaning
Cleaning of main nozzle, relay nozzle, air filter, hose pipes etc. ultra sonic cleaning is important to maintaining the efficiency of weaving.
It should avoid the damaged or error portion of the surface so such condition of deposition is micro fiber can drop the pressure of air blowing through it so these can be avoided due to these cleaning.
Opening & closing timing of nozzle
Correction made delayed opening loss pressure through valve enhance the efficiency of machine. Early opening will reduce the air consumption. Improper opening & closing timing of valves lead to undue stress on yarn thereby leading to break.
After proper adjustment the no. of end breaks can be reduced. The air consumption can be reduced up to 5 to 6%.
Pressure on the nozzle
Pressure on nozzle has more impact on the m/c performance. Improper pressure adjustment will causes the weft stop during working so quality & productivity can be minimized. To avoid the problem, proper setting of pressure can be required. These can be adjusted according to count, rpm, width of m/c. Proper combination between main & relay nozzle will reduce the air consumption.
Setting of nozzle
1- Distance between two nozzles - Improper setting between to relay nozzle will cause to variation in air pressure and will cause m/c performance to be in decreasing the air consumption will be unnecessary increases.
2- Nozzle height – P
roper height setting of relay nozzle will causes reduction in air pressure during weft insertion & air consumption can be reduced. Proper setting of the nozzle height will provide the uniform displacement of yarn during insertion.
1- Distance between two nozzles - Improper setting between to relay nozzle will cause to variation in air pressure and will cause m/c performance to be in decreasing the air consumption will be unnecessary increases.
2- Nozzle height – P
3- Nozzle angle- For uniform weft insertion of yarn during insertion proper nozzle angle will reduce air consumption. Pressure required for insertion can be reduced.
Multi hole versus single hole
The multi hole relay nozzles guarantee a very stable blowing angle at different pressure levels. This is recommended for style changes that require different relay nozzle pressure settings. The single-hole nozzles need to be adjusted by hand whereas multi-hole nozzles keep their blowing angle stable and do not need any adjustment or fine tuning. Due to the pre-given horizontal and vertical jetting angles, the multi-hole nozzle requires less space between the warp yarns, which prevents nozzle marks in your fabric.
The multi hole pattern allows also a more efficient air stream, thus delivering a better performance over single hole nozzles, giving up to 15% higher yarn speed for the same air consumption. Single-hole nozzles are recommended in case of a dusty environment or low air quality.
Multi hole versus single hole
The multi hole relay nozzles guarantee a very stable blowing angle at different pressure levels. This is recommended for style changes that require different relay nozzle pressure settings. The single-hole nozzles need to be adjusted by hand whereas multi-hole nozzles keep their blowing angle stable and do not need any adjustment or fine tuning. Due to the pre-given horizontal and vertical jetting angles, the multi-hole nozzle requires less space between the warp yarns, which prevents nozzle marks in your fabric.
The multi hole pattern allows also a more efficient air stream, thus delivering a better performance over single hole nozzles, giving up to 15% higher yarn speed for the same air consumption. Single-hole nozzles are recommended in case of a dusty environment or low air quality.
The perfect nozzle for any Air jet loom
Over 40 years ago, Te Strake Textile revolutionized weaving with the introduction of its unique air jet weaving system. Today, Te Strake Textile is worldwide recognized as the trendsetter and innovator in air insertion technology. With their complete range of relay nozzles, Te Strake Textile delivers the perfect relay nozzle for your needs, no matter which loom type you are using.
Innovation for better weaving performance
D-type relay nozzle
Based on their extensive experience in air insertion technology, Te Strake Textile takes another step in air jet weaving with its innovative D-type nozzle. This D-type nozzle incorporates unique characteristics to outperform any other model in terms of:
• Reduced weft stops
• Improved machine performance
• Extra stability of nozzle body
• Prevention of nozzle marks
• Reduction of air consumption
• Increased lifetime
Unique body design
The new design makes the D-type nozzle the most robust and stable nozzle currently available, with up to 45% higher resistance to deformation. This stronger nozzle requires an absolute minimum of adjustments for higher productivity.
New nozzle head
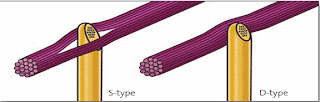
With the successful experience of a round or convex nozzle head, the D-type nozzle head has been further optimized for better fabric quality. Filamentation, nozzle marks or having your warp yarns staying on top of the nozzle, belong now to the past.
Different hole patterns
The D-type nozzle is available with different hole patterns (1 – 7 – 16 – 19 holes) to suit your specific need. The highest performance is given by the 16 hole nozzle, offering you specific benefits.
Different types of nozzles
B – TYPE
D-TYPE
C-TYPE
S-TYPE
Insertion time
With the revolutionary 16-hole pattern, the air stream is now perfectly parallel to the warp yarns, thus making maximum use of the insertion time. As a result, higher weaving speed for increased productivity or a gentler yarn passage for better fabric quality is guaranteed.
Higher performance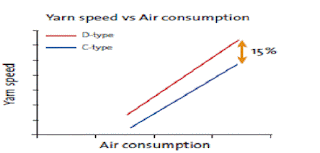
The D-type 16 hole nozzle can offer you significant cost savings. This nozzle can generate the same yarn speed with less air consumption – in some cases up to 15 – 20 % depending on the weaving condition. Either, with the same air consumption, you are able to increase the yarn speed.
With the revolutionary 16-hole pattern, the air stream is now perfectly parallel to the warp yarns, thus making maximum use of the insertion time. As a result, higher weaving speed for increased productivity or a gentler yarn passage for better fabric quality is guaranteed.
Higher performance
The D-type 16 hole nozzle can offer you significant cost savings. This nozzle can generate the same yarn speed with less air consumption – in some cases up to 15 – 20 % depending on the weaving condition. Either, with the same air consumption, you are able to increase the yarn speed.
DLC Coating
The D-type nozzles are exclusively coated with Diamond-Like carbon coating which is superior to any other coating. It increases life time up to 5 times and avoids wear and yarn cuts. DLC coating is therefore specially recommended for abrasive warp yarns.
Control of sub-nozzles
The D-type nozzles are exclusively coated with Diamond-Like carbon coating which is superior to any other coating. It increases life time up to 5 times and avoids wear and yarn cuts. DLC coating is therefore specially recommended for abrasive warp yarns.
Control of sub-nozzles
Control of sub-nozzles by increased groups conventionally, as in Fig. 02; sub-nozzles are arranged in groups of 4 nozzles. An electro-magnetic valve is attached to each group and the sub-nozzles of the same group jet simultaneously. Tsudakoma’s new arrangement, as in Figure 3, has an electro-magnetic valve with a smaller inner volume so that it matches to 2 sub-nozzles. The control of valve is improved, and extra jetting time is reduced.
Improvement of nozzle for feeding the filling and reed
A Laval-type nozzle: the interior is wider at one end than the other. The nozzle’s pulling force is increased by 30%, and air consumption of the main nozzle is reduced by 10%. (Compared with the cylindrical nozzle) In addition, the sub-nozzles use almost all of the air consumption in the air jet loom because of their number. Tsudakoma invented a new sub-nozzle. The part around the jetting outlet of the new sub-nozzle is hollowed (See Figure 5), and the flow speed is increased by 10%. Because the filling does not touch the edge of the jetting outlet, damage to the filling is lowered. For the reed, the air guide of the reed for feeding the filling is narrowed, and the air flow speed is raised.
No comments:
Post a Comment