Air-jet Filling Insertion System
In air-jet weaving machines, the filling is inserted pneumatically and a typical filling insertion system is shown in figure. The filling yarn is carried through the shed by compressed air flow supplied from the main nozzle and relay nozzles.
The timing of jet activity should be controlled in such a way that the main nozzle is supplied with compressed air from the beginning of the weft insertion phase and the relay nozzles also receive compressed air in synchronization with the projected end of the weft .
In air-jet weaving machines, the filling is inserted pneumatically and a typical filling insertion system is shown in figure. The filling yarn is carried through the shed by compressed air flow supplied from the main nozzle and relay nozzles.
The timing of jet activity should be controlled in such a way that the main nozzle is supplied with compressed air from the beginning of the weft insertion phase and the relay nozzles also receive compressed air in synchronization with the projected end of the weft .
The main nozzle and each group of sub-nozzles are operated individually by magnet valves and electronic pulse. Each nozzle is operated at a different instant of time but each of them overlaps slightly in air supply .Air pressure and blow duration of the main nozzle and sub-nozzle groups can be adjusted as required.
Experimental Details
The Effect of Relay Nozzle Diameter
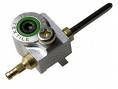
In the first part of the work, previously used relay nozzles with 1.4 mm hole diameter were replaced with the relay nozzles of 1 mm hole diameter. The reason for selection of the relay nozzles with 1 mm diameter was that they were the only available nozzle diameters in the weaving mill during the study. With this replacement, air consumption was reduced by 21% while a slight increase in loom efficiency, which is the ratio of net loom running time to the total time spent for production, was obtained. However, the increase in loom efficiency was not statistically important.
Effect of Relay Nozzle Blowing Times
In this part of the work, a truly experimental study was conducted to optimize the blowing times on Picanol looms. Firstly, the average increase in air consumption with the increase of blowing time was determined. Then the minimum blowing time that enables both problem-free weaving and the same loom efficiency level to be maintained was determined.
The Effect of Number of Relay Nozzles Hole 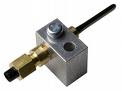
A significant change in air consumption was not observed after replacement of the 19-holed relay nozzles with the 16-holed ones. Therefore, weaving mills are recommended to search for the best multi-holed relay nozzle type for their applications followed by optimization of blowing times before the replacement takes place.
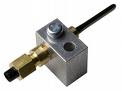
A significant change in air consumption was not observed after replacement of the 19-holed relay nozzles with the 16-holed ones. Therefore, weaving mills are recommended to search for the best multi-holed relay nozzle type for their applications followed by optimization of blowing times before the replacement takes place.
In conclusion, this study showed that weaving mills could obtain considerable savings in energy costs by working with single-holed relay nozzles having smaller hole diameter and by achieving the shortest possible blowing time adjustments on air-jet looms equipped with multiholed relay nozzles, without any decrease in loom efficiency and performance.
No comments:
Post a Comment